Low Voltage PVC vs. XLPE Power Cables: Which Is Ideal for Your Project?
Time: 2025-07-23 01:35:01
Source: Henan Province Jianyun Cable Co., Ltd.
Low voltage power cables, typically rated at 0.6/1kV, are essential for distributing electricity in residential, commercial, and industrial projects. Two common insulation materials for these cables are polyvinyl chloride (PVC) and cross-linked polyethylene (XLPE). Each offers distinct advantages and limitations, making the choice dependent on project-specific requirements such as environmental conditions, safety standards, and cost considerations. This guide compares PVC and XLPE low voltage power cables, detailing their properties, applications, and selection criteria to help determine the ideal choice for your project, presented in a formal and structured manner.
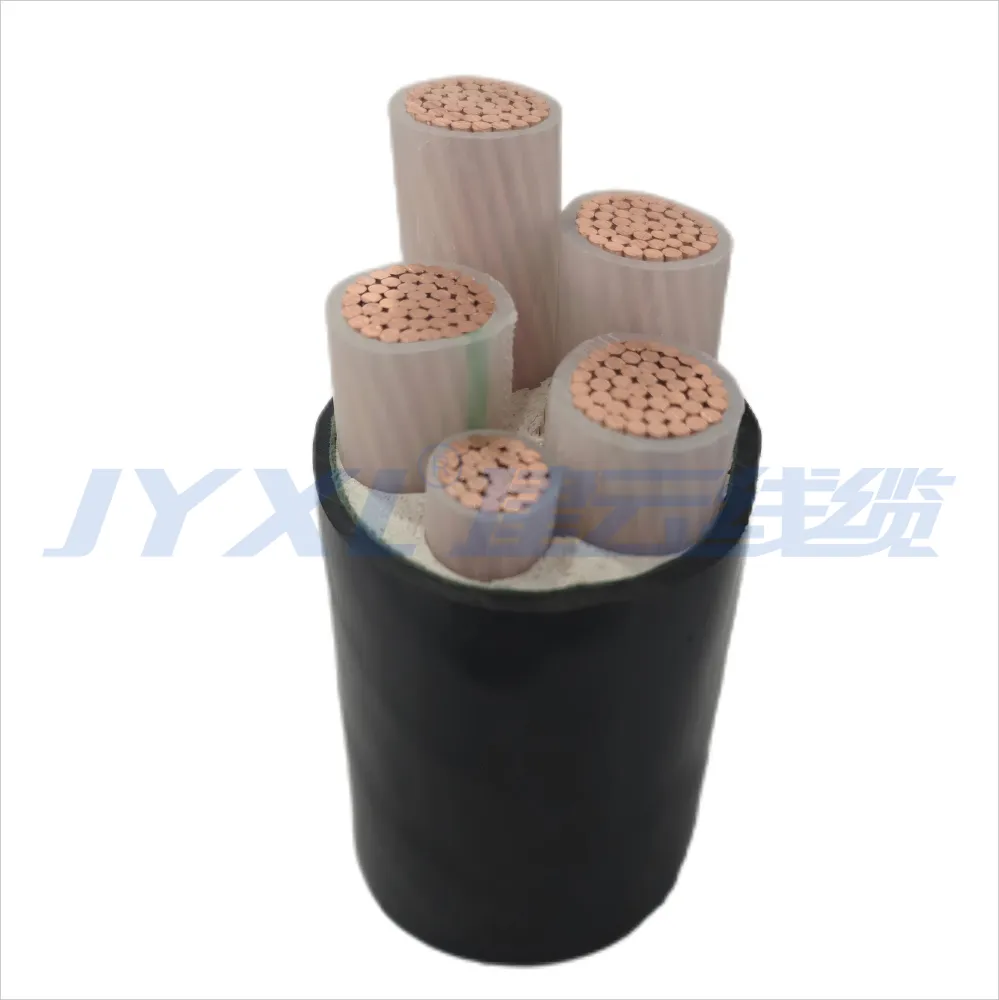
Table of Contents
1. Overview of PVC and XLPE Cables
Low voltage power cables are designed to transmit electricity at voltages up to 1kV, commonly used for lighting, machinery, and building power systems. The insulation material significantly impacts performance, durability, and safety.
-
PVC Cables: Use polyvinyl chloride as insulation and sheathing material, known for cost-effectiveness and versatility in general-purpose applications.
-
XLPE Cables: Use cross-linked polyethylene insulation, offering superior thermal, electrical, and environmental performance for demanding conditions.
2. Key Properties of PVC and XLPE Cables
2.1 PVC Power Cables
-
Material Composition: Thermoplastic PVC insulation and sheathing, with copper or aluminum conductors.
-
Temperature Range: Typically -15°C to 70°C (some up to 90°C with special formulations).
-
Electrical Properties: Good dielectric strength, suitable for low voltage applications, but higher dielectric losses compared to XLPE.
-
Environmental Resistance: Moderate resistance to moisture, UV, and chemicals; less durable in extreme conditions.
-
Mechanical Properties: Flexible and easy to handle, but less resistant to abrasion and mechanical stress unless armored.
-
Fire Performance: Emits toxic fumes (e.g., hydrogen chloride) during fire; requires LSZH variants for enhanced safety.
-
Cost: Generally lower cost due to simpler manufacturing.
-
Standards: IEC 60502-1, UL 83, EN 50525.
2.2 XLPE Power Cables
-
Material Composition: Thermoset XLPE insulation with PVC, PE, or LSZH sheathing, and copper or aluminum conductors.
-
Temperature Range: -40°C to 90°C (up to 120°C for short periods), suitable for higher operating temperatures.
-
Electrical Properties: Superior dielectric strength and lower dielectric losses, improving efficiency in power transmission.
-
Environmental Resistance: Excellent resistance to moisture, UV, chemicals, and thermal stress, ideal for harsh environments.
-
Mechanical Properties: Higher resistance to abrasion and mechanical stress, especially when armored.
-
Fire Performance: Can be paired with LSZH sheathing for low-smoke, low-toxicity performance; inherently more heat-resistant than PVC.
-
Cost: Higher initial cost due to complex cross-linking process.
-
Standards: IEC 60502-1, UL 44, EN 50395.
3. Applications and Suitability
3.1 PVC Cable Applications
-
Residential Buildings: Powering lighting, outlets, and small appliances in homes and apartments.
-
Commercial Facilities: Indoor power distribution for offices, retail spaces, and low-demand systems.
-
Light Industrial Use: Small machinery and equipment in controlled environments with minimal chemical or thermal exposure.
-
Temporary Installations: Construction sites or portable equipment due to flexibility and low cost.
-
Limitations: Not ideal for high-temperature environments, outdoor exposure without UV-resistant sheathing, or areas requiring stringent fire safety (unless LSZH).
3.2 XLPE Cable Applications
-
Industrial Plants: Powering heavy machinery, motors, and automation systems in harsh conditions.
-
Outdoor Installations: Underground or exposed applications, such as street lighting or renewable energy projects, due to UV and moisture resistance.
-
High-Temperature Environments: Areas near heat-generating equipment or in hot climates.
-
Safety-Critical Areas: Facilities requiring LSZH cables for fire safety, such as tunnels, metro systems, or hospitals.
-
Limitations: Higher cost may be prohibitive for low-budget projects with minimal environmental challenges.
4. Comparison of PVC and XLPE Cables
Property
|
PVC Cables
|
XLPE Cables
|
Temperature Range
|
-15°C to 70°C
|
-40°C to 90°C (up to 120°C short-term)
|
Dielectric Strength
|
Good
|
Superior, lower losses
|
Environmental Resistance
|
Moderate (moisture, UV, chemicals)
|
Excellent (moisture, UV, chemicals, thermal)
|
Mechanical Durability
|
Moderate, requires armoring for stress
|
High, enhanced with armoring
|
Fire Performance
|
Toxic fumes, requires LSZH for safety
|
Heat-resistant, LSZH options available
|
Cost
|
Lower
|
Higher
|
Applications
|
Residential, commercial, light industrial
|
Industrial, outdoor, safety-critical
|
Standards
|
IEC 60502-1, UL 83, EN 50525
|
IEC 60502-1, UL 44, EN 50395
|
5. Selection Criteria for Your Project
Choosing between PVC and XLPE cables depends on project-specific factors:
-
Environmental Conditions: Select XLPE for outdoor, underground, or high-temperature environments due to its superior resistance to moisture, UV, and heat. Use PVC for indoor, controlled environments with minimal exposure.
-
Safety Requirements: Choose XLPE with LSZH sheathing for areas with strict fire safety regulations (e.g., public buildings, tunnels). PVC with LSZH is viable but less heat-resistant.
-
Budget Constraints: Opt for PVC cables in cost-sensitive projects with low environmental or thermal demands, such as residential wiring. XLPE is justified for long-term reliability in demanding applications.
-
Installation Type: PVC cables are suitable for conduit or indoor installations due to flexibility. XLPE is preferred for direct burial or exposed installations with armoring.
-
Power Efficiency: Use XLPE for longer cable runs or high-load applications to minimize dielectric losses and improve efficiency.
-
Regulatory Compliance: Ensure cables meet relevant standards (e.g., IEC 60502-1, EN 50575 for CPR in EU) based on project location and application.
-
Maintenance and Lifespan: XLPE cables offer a longer service life (typically 25–40 years vs. 15–25 years for PVC), reducing maintenance costs in critical infrastructure.
6. Conclusion
Both PVC and XLPE low voltage power cables serve essential roles in power distribution, but their suitability depends on project requirements. PVC cables are cost-effective and versatile for residential, commercial, and light industrial applications with controlled environments. XLPE cables excel in harsh conditions, offering superior thermal, environmental, and electrical performance, making them ideal for industrial plants, outdoor installations, and safety-critical areas. By evaluating environmental conditions, safety needs, budget, and regulatory requirements, project managers can select the optimal cable type to ensure reliability, safety, and efficiency for their specific application.